Well-protected winter building sites

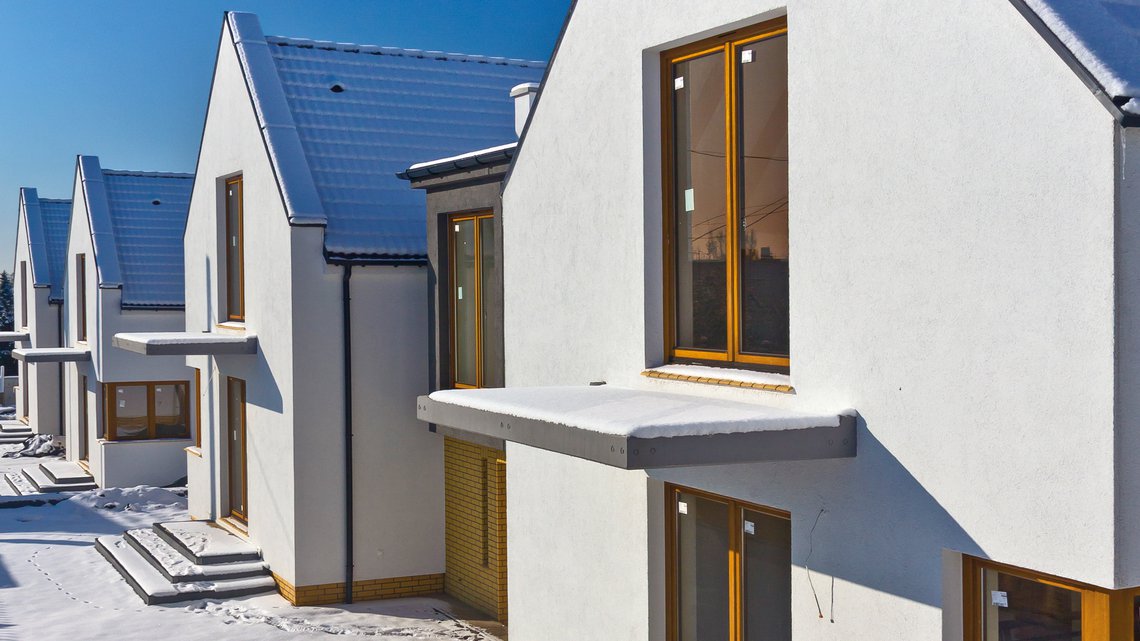

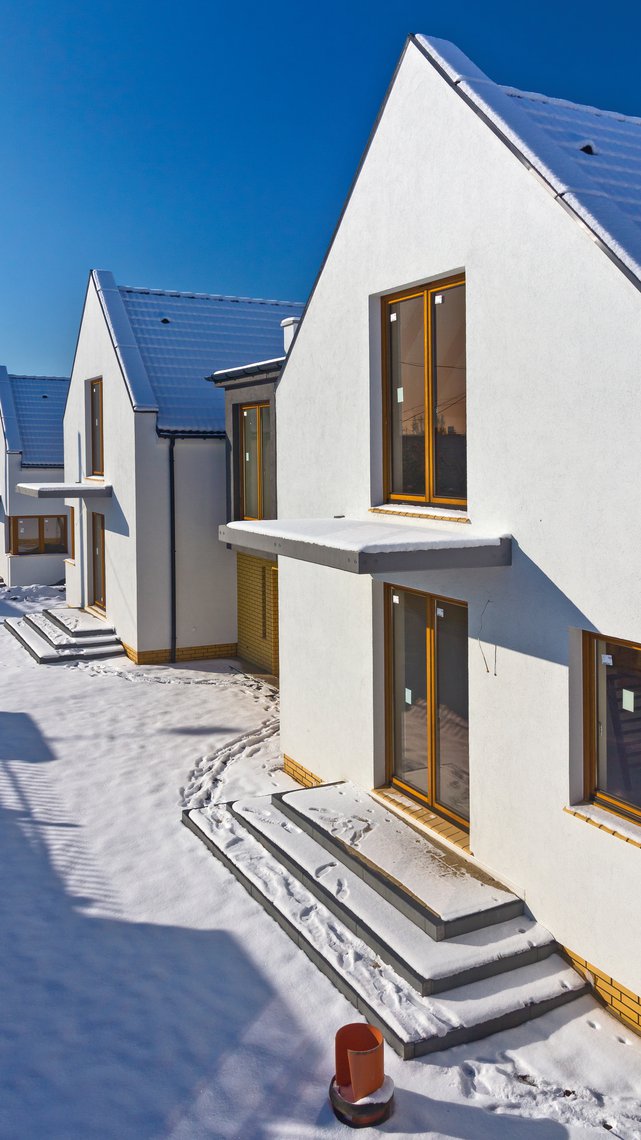
Winter
building
sites
Thermal insulation and airtightness seals can be installed professionally on building sites even in wintertime! pro clima’s humidity-variable membranes are more impermeable to diffusion in winter and can reliably protect insulation against mould and damage to structures caused by moisture penetration.
Their diffusion resistance is sufficiently high even for short-term peaks in moisture associated with building activity. In summer, these membranes can become very permeable, thus ensuring the best possible conditions for drying-out to the inside. Conventional vapour control membranes with constant diffusion resistances do not offer this additional protection.
Not every humidity-variable membrane is suitable for winter building sites
With humidity-variable vapour control membranes, winter construction sites are not a problem as long as these membranes have the right hydrosafe value.
The hydrosafe value specifies how well sealed a humidity-variable vapour retarder still is at an average humidity of 70%.
Average humidity of 70% will be present if there is 90% indoor air humidity and 50% humidity in the space between the rafters, for example; this level of humidity can occur when installing screed or plastering walls.
The right hydrosafe value is crucial!
A vapour control (or vapour check/retarder) membrane must have a hydrosafe value of between 1.5 m and 2.5 m in order to protect structures against dampness even in the case of the increased relative humidity that can be present during construction work. The requirement that sd > 1.5 m and < 2.5 m is stipulated in the DIN 68800-2 standard and is described in further detail by the so-called 70/1.5 rule.
pro clima’s humidity-variable INTELLO and DB+ membranes fulfil these requirements reliably. As a result, they provide dependable protection for structures over their entire service lives – even on winter construction sites.
pro clima membranes have been providing reliable protection for decades
pro clima DB+ was developed in the early 1990s with the aim of ensuring a high level of moisture protection during the construction phase and after buildings have been completed too. DB+ has been systematically refined to create INTELLO. Millions of square metres of these two membranes have been successfully installed on building projects.
With INTELLO and DB+, building structures are protected both during and after the construction phase.
Shorter construction period – Greater care
In the past, there was less activity in the construction industry in Germany in wintertime. This has changed, and planning, construction and insulation are now carried out all year round! As a dry method of construction, timber construction has clear advantages in this regard, as increased building moisture does not need to be taken into account. In contrast, masonry construction does not allow for sufficient time for the removal of excess building moisture due to the speed of construction progress; as a result, increased dampness occurs in surrounding building materials that would otherwise have remained dry.
A careful, coordinated approach by all participating parties is necessary in order to construct reliable, well-protected structures even under these more challenging conditions in wintertime. This approach includes not just planning of the structure at all levels, but also coordination among all trades with regard to schedules and the work carried out.
Planning for the right construction sequence
Before moisture is introduced into the building as a result of plastering or installing screed, the insulation should be installed into the spaces between the rafters and the vapour control layer should be sealed in an airtight manner.
The building should initially not be ventilated to allow the screed to harden without deformation or the formation of cracks. Depending on the type of screed used, the removal of building moisture can generally be initiated after just three days. This should then be done in a systematic, effective manner.
However, it is often the case that this moisture is not dried using drying equipment and is not removed by ventilation. If drying and ventilation are not carried out, a “tropical climate” can occur inside the building that can soon have a negative impact on a range of structural elements.
For this reason, the issue of increased moisture during the construction phase is now also dealt with in standards: for example, DIN 4108-7 states that increased construction moisture is to be removed from buildings and/or that drying equipment is required.